What’s in a Wall? More than you might think.
The primary function of a wall is to separate environments: keep the outside out, and the inside in. Historically, we relied on single materials to construct our walls –timber or stone– and we didn’t expect much from them other than to hold up our shelters.
Today, we expect our walls to perform better: we expect them to keep us dry, to keep us healthy, and to keep us warm. To do this well, walls need to control the flow of water, air, vapour, and heat. We have yet to invent a single building material that can reliably perform all of these functions, which is why we rely on assemblies of materials to comprise our walls. Wall assemblies are constructed to serve the following functions (listed in order of importance):
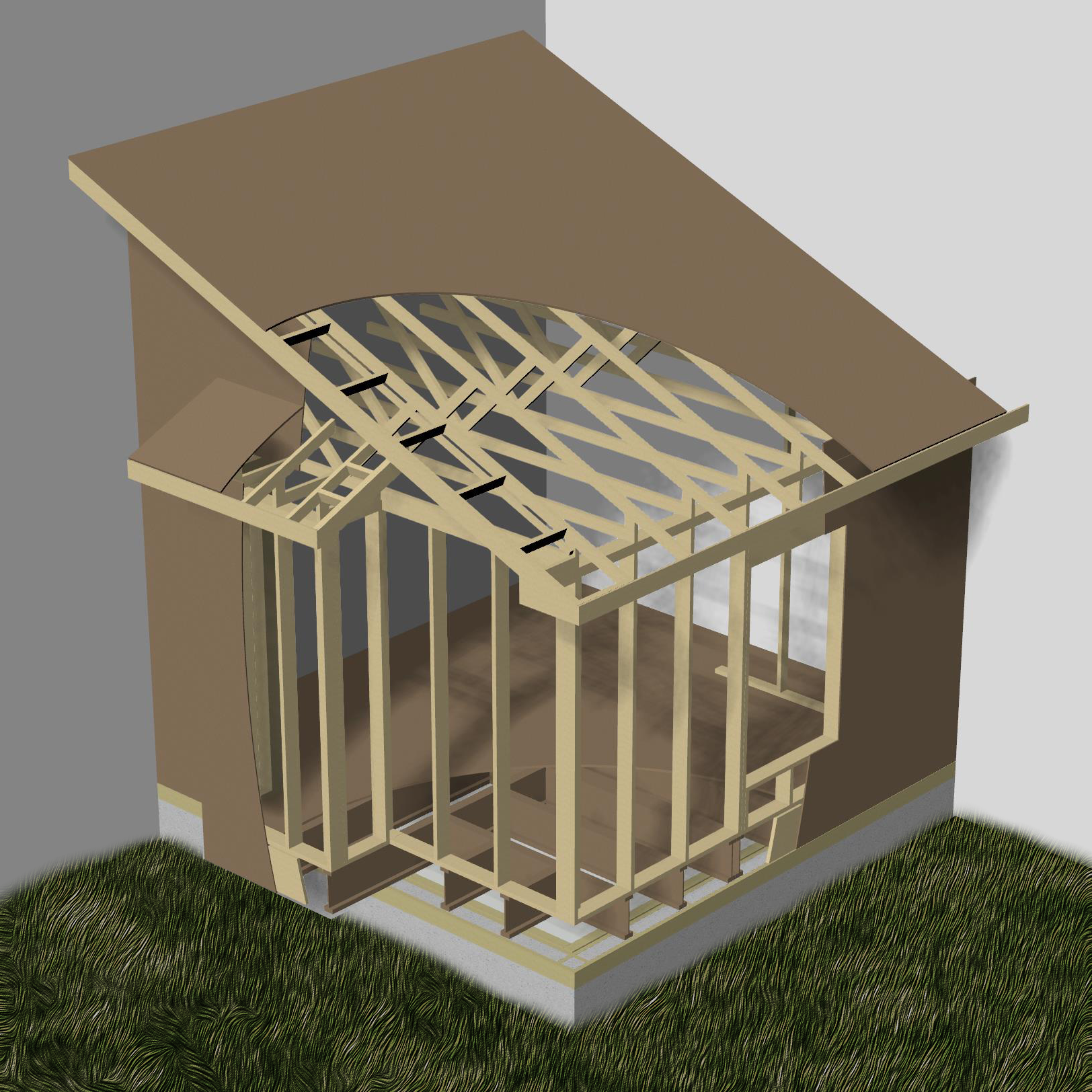
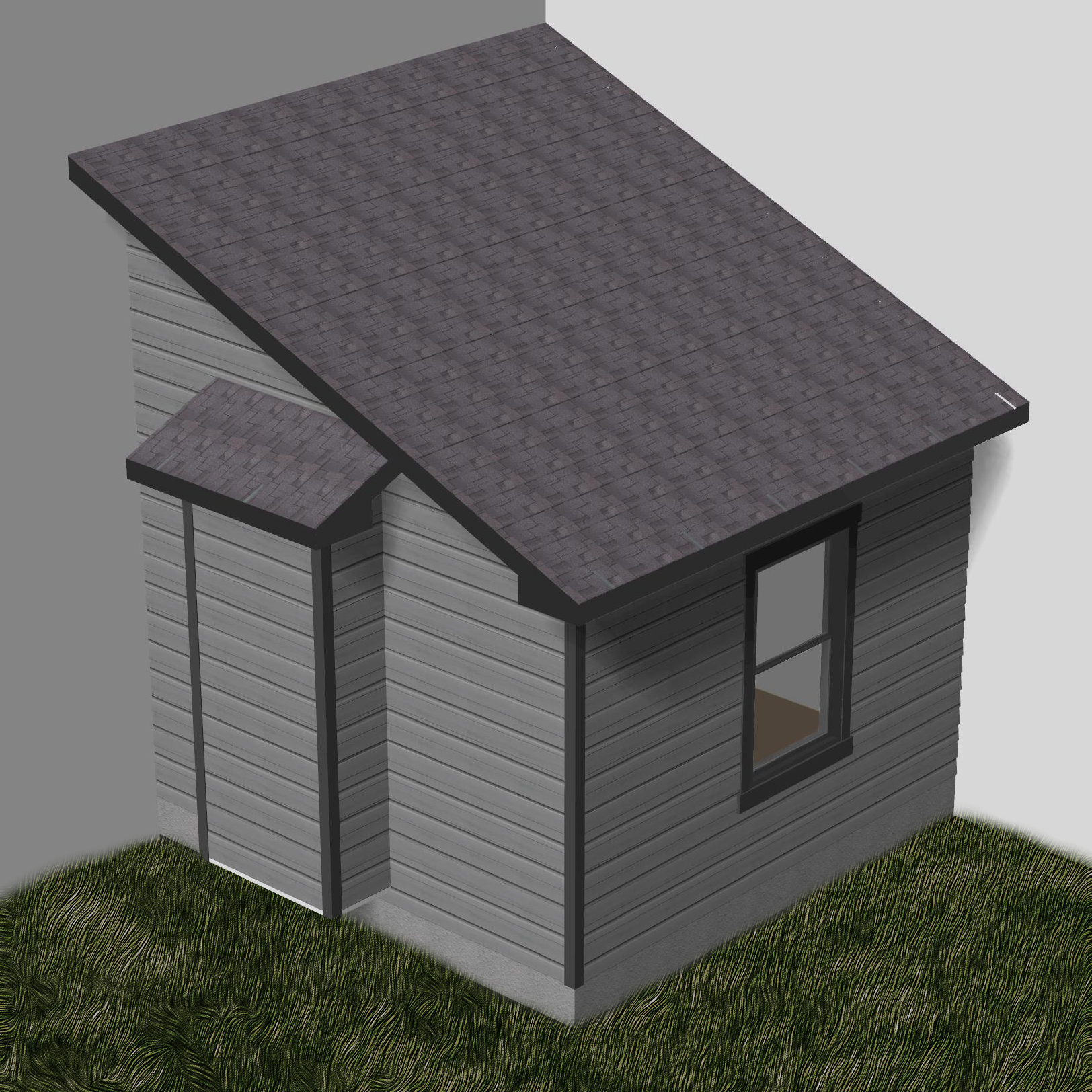


Structure
Without a structural element walls couldn’t stand up, let alone hold the floors and/or roofs above to prevent collapse. The structure can be provided by a number of materials, including wood, steel, concrete, brick, rammed earth, or even hay bales. The structure simply needs to withstand the live loads of the occupants, the dead loads of the structure itself, and resist environmental forces like gravity and wind.
Water Control
Other than the structure, water control is the most important function of the wall assembly. Typically thought of as the decorative exterior cladding (e.g.: siding, stucco, brick, etc.), this layer is the first line of defense against the elements, responsible for shedding rainwater and keeping the rest of the building dry. If this outer layer fails and you get leaks, there’s no point worrying about the remaining functions.
Air Control
A leaky house can cause a number of problems from cold air drafts and wasted heat energy to mould and rot. Air leakage can also bring in dust and harmful gasses, such as carbon monoxide from attached garages. This is why we aim to make our homes air-tight. Air control can be achieved using a single or combination of materials, such as an exterior membrane, sheathing wrap, or even just the drywall.
Vapour Control
Not to be confused with air or water controls, vapour control is about preventing the diffusion of aerosols through the wall assembly. In Alberta, as vapour moves through a wall from a home’s warm high-humidity environment to the outdoor cooler low-humidity environment, it will condense and trap moisture within the assembly. This moisture will transfer heat out of the house and, if it doesn’t dry out quickly, will lead to mould or rot. To prevent these issues, vapour barriers in the form of plastic films or membranes are used to reduce vapour permeability of the assembly.
Thermal Control
The last function a wall needs to perform is to insulate the interior environment from the outside world. In Alberta for most of the year, this means we aim to slow the transfer of heat by using some form of insulation. One can use virtually any air-trapping material to insulate –like crumpled newspaper or shredded denim– but results vary widely between materials. The most common and effective materials used today are fibreglass or mineral-wool batts, blown-in cellulose, or rigid foam plastics like polyisocyanurate (PIR), extruded polystyrene (XPS), expanded Polystyrene (EPS) or spray-applied polyurethanes (open or closed-cell).*
* Insulation performance is measured by its thermal resistance —imperial R-values, or metric RSI units. The listed materials range from R3.5-R6 per inch, or RSI 0.02-0.04 per millimetre. For reference, wood studs are about R1 per inch, or RSI 0.007 per millimetre.
Cut-away diagram of traditional assemblies
Putting it all together.
Conventional wood-frame construction in North America builds walls out of dimensional lumber studs sheathed with plywood or oriented strand board (OSB) to provide the structure. The exterior is clad with siding or stucco to provide the water control layer. Between the cladding and the structure, the wall is covered with a sheathing wrap, like Tyvek or Typar, to provide the primary air control layer.
Inside, the wall is wrapped with a polyethylene (“poly”) film then sealed or taped to provide the vapour barrier, which also helps to hold the fibreglass batt insulation in its place between the studs for thermal control. The interior is then finished with mudded-and-taped gypsum board and paint, which acts as a backup air control.
Using 2x6 studs and R20 (RSI 3.5) batt insulation, this assembly yields an effective ~R14 (RSI 2.46) wall when factoring in all components together. While there are a number of variations to this conventional wall to improve its performance (such as double- or staggered-studs, advanced framing techniques, or more efficient insulation), this arrangement of the control layers is fundamentally flawed, and it’s time we do better.
What’s wrong with conventional walls?
The primary issue with conventional walls is the structure spanning the entire width of the assembly, bridging the cold outside with the warm inside. These bridges greatly reduce the thermal control of the wall by interrupting the insulation with a cold spot every 16-24” (400-600mm). The fluctuation in temperatures throughout the year can also cause the structure to expand and contract, leading to cracks that let air and moisture move through.
Thermal bridges are also magnets for vapour to condense within the wall cavity. Vapour inevitably makes its way in because poly is never sealed well enough, especially around floor-to-wall connections or electrical outlets. Traditionally, we’ve just hoped the moisture evaporates, leaving through the same holes before any damage is done —a risky bet for sure.
Outside, in Alberta’s harsh climate, the cladding needs to be durable enough to withstand high temperature swings, heavy snowfall, and hail in order to properly control water —just look at the damage done to vinyl siding in Calgary’s summer 2020 storm. If the cladding is compromised, or simply ineffective, it doesn’t take much to then tear into the underlying sheathing wrap meant to control the flow of air. With an open invitation for weather to penetrate the assembly, heat will be lost while moisture accumulates behind the wall’s surfaces, aiding the growth of mould and weakening the structure unbeknownst to the homeowner.
How can we do better?
Many new approaches to wall construction now exist to combat the shortfalls of convention, such as structural insulated panels (SIPs) or insulated concrete forms (ICFs). While these new systems are certainly improvements –virtually eliminating thermal bridging– they can be expensive, present design limitations, and require highly specialized construction personnel.
Of the options that utilize more conventional construction methods, there are two that follow very similar principles: REMOTE (Residential Exterior Membrane Outside insulation TEchnique) and PERSIST (Pressure Equalized Rain Screen Insulated Structure Technique). These techniques each apply a very simple concept: keep the control layers outside of the structure so they act as a continuous blanket around the home, protecting the structure from temperature fluctuations and providing a single continuous plane on which to seal the house from the elements. This concept has been coined by building scientist, Joseph Lstiburek, as “The Perfect Wall”.
Using this concept, the efficiency of the insulation is significantly increased as there are no longer any thermal bridges, and the structure no longer expands or contracts since it stays within the conditioned space. With all the control layers grouped outside the structure to create a clear demarcation between environments, there’s nowhere for moisture to hide or collect.
Where is construction headed?
With advances in building systems like SIPs and ICFs, and techniques like REMOTE and PERSIST, the construction industry has the tools to build long-lasting, high-performance homes. The trouble to implementing these methods as standard is the added cost of doing anything new. But with recent and upcoming updates to the National Building Code of Canada (Alberta Edition), as well as the increased performance targets of the National Energy Code of Canada for Buildings, the housing industry is being forced to look into new ways to implement these high-performance techniques while keeping costs down.
In my next blog post, I’ll be taking a closer look at The Perfect Wall to see how best to apply its principles to Alberta’s climate.
If you would like to get ahead of the curve and depart from the usual methods of construction for your next build, Deviate Design can help!